Toray KP Films offers products of the high quality through its Vacuum Deposition technology,
slit processing, and KP seduce materials.
HOME > Technology review
- Vacuum Deposition
- Slit
- Surface improvement
- Coating
- Laminate
- Vacuum Deposition film for Capacitors
- Vacuum Deposition film for magnetic wave shields
- Vacuum Deposition film for printed boards
- Vacuum Deposition film for ultra-thin foil transfer
- Vacuum Deposition film for ECM
- Vacuum Deposition film for electric cables
- Vacuum Deposition film for decorative uses
- Heat-resistant coating film for electric cables
- Masking tape for Capacitors
- Heat-resistant hot melt grew coated tape
Technology review - TECHNOLOGY
Vacuum Deposition film for Capacitors
There are three processes involved in the manufacture of Vacuum Deposition film for Capacitors: the Vacuum Deposition process, the slit process, and the inspection process.
The Vacuum Deposition process creates the Vacuum Deposition film quality. The slit process finishes the product, while rigorous inspection process enables it to be used by the customer.
The Vacuum Deposition process
- Vacuum Deposition deposits the following on films:
- Polyethylene terephthalate (PET)
- Polypropylene (PP)
- Polyphenylene sulfide (PPS)
- Polyimide (PI)
- Aramid
- It also deposits mainly
- aluminum, zinc, and copper on metals.
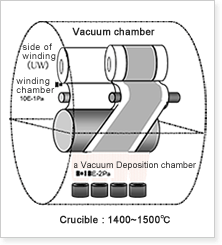
The interior of a Vacuum Deposition machine is divided into a winding chamber and a Vacuum Deposition chamber. Metal is heated in a high vacuum, promoting evaporation. This enables the adherence of the substance on the surface of the plastic film.
A high vacuum means there is pressure surrounding the area that creates an aurora in the space (Height: 100 to 300 km).
A Vacuum Deposition film thickness from 100 Å to 20,000 Å is possible. (10nm to 2,000 nm)
We have three different methods for heating metal to be deposited.
They are:
- High-frequency induction heating method
- Resistance heating
- Electron beam
A margin, or a portion on which there is no Vacuum Deposition, is required for using metallic Vacuum Deposition film as a Capacitor. The function for forming this margin is incorporated in the vacuum Vacuum Deposition machine.
The metal heating method
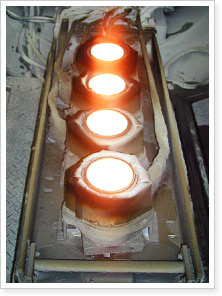
The high-frequency induction heating method
The metal is melted by heating it to approx. 1,400 to 1,500°C in a crucible.
A magnetic field is created by passing a current through the coil, and the crucible is heated.
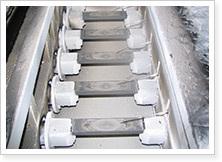
Resistance heating method (Energized heating method)
A boat is heated and aluminum wire is continuously fed into it, resulting in Vacuum Deposition.
The metal is heated by energizing the BN composite material, which is both corrosion-proof and conducts electricity.
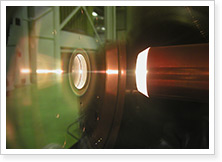
Electron beam method
The metal is heated by focusing an electron beam directly onto the vapor deposit metal. Unlike the other methods, the crucible or the boat is not heated.
Vacuum exhaust systems of Vacuum Deposition machinery
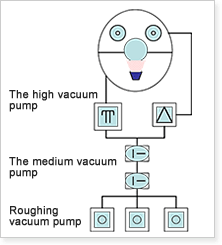
Vacuum exhaust systems of Vacuum Deposition machinery
This achieves the high vacuum ideal for Vacuum Deposition by dividing the exhaust system into three stages.
- ・The high vacuum pump
- The pump creates a high vacuum that enables the formation of a uniform Vacuum Deposition layer on the film.
- ・The medium vacuum pump
- A relay pump that conveys the action to the high vacuum pump
- ・Roughing vacuum pump
- A pump that begins evacuation from the outer air
Vacuum Deposition machinery (Winding type)
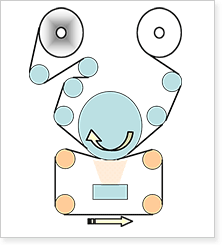
The film is fed into the Vacuum Deposition chamber by running it through the flattening roller underneath the CC-1 (cooling roll) from the unwinding side. After the Vacuum Deposition process is finished, the film is cooled and rewound through the flattening roller.
Vacuum Deposition is possible starting from 1 µm of the thinnest film thickness.
Margin process I / Oil margin
- Our expertise resulted in the creation of oil margin technology.
- The process enables a minimum product width of 2.25 mm, with a 0.25 mm margin.
- We use liquid chromatography to measure the adhesion volume.
Margin process II / Margin tape
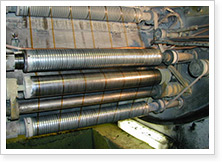
In general, polyimides are used as the margin tape material. The tape revolves endlessly.
Quality control
Control of Vacuum Deposition film resistance
- Film resistance is measured during Vacuum Deposition by the two-terminal method.
- The extent of film resistance uniformity is controlled by passing a light through the film during Vacuum Deposition and measuring its penetration rate.
- Adjusting the film resistance during Vacuum Deposition is done by adjusting the output of the evaporation source to make the evaporation volume uniform.
The most advanced pattern technology
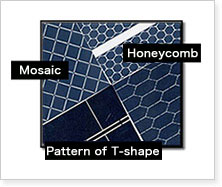
- We are capable of handling Vacuum Deposition for all types of patterns to improve safety and electric potential gradient.
- We are now also able to handle more complex and detailed patterns with our improved pattern roll technology.
Now preparing content
We are now preparing the content for this section, so please wait a little bit longer.
For more detailed information, feel free to make an inquiry on our inquiry page .
Now preparing content
We are now preparing the content for this section, so please wait a little bit longer.
For more detailed information, feel free to make an inquiry on our inquiry page .
Slitted products are used for…
Our slitted products are used in a variety of everyday situations.
- Capacitor films of all types, including home appliances, PCs, and hybrid cars
- Computer backup tape
- Ultra-thin electromagnetic wave shield wire
- Optical liquid crystal display reflecting film
- Carrier tape
What will be demanded of slitted products in the future
Many different products use the slitter, and we also respond to a diversity of requests.
- Product quality
- Width accuracy
- Winding form
- Larger diameters
- Processes adding value to existing film
Our broad based response allows us to select the model best suited to the wide-ranging demands of our users, in fields as varied as electronics, information, electrical equipment, and healthcare.
Slit process
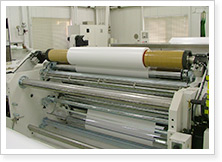
We have 19 slitting machines.
Our advanced slitting technology meets the needs of our customers.
Microslitting machines
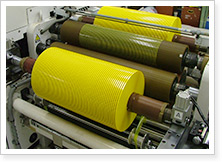
- 1)Uses
- Capacitor film, release film, compound film, insulation film, magnetic tape, carrier tape
- 2)Characteristics
- We have demonstrated our successful performance in accuracy and quality control by achieving a slit process for optional narrow widths (as narrow as 3.5 mm) for ultra-thin film.
The micro-slit is the achievement of which we are the most proud in our company’s history.
Large slitting machines
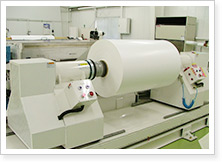
- 1)Uses
- Optical and reflecting film, release film, packaging film, carrier film for all types of processes
- 2)Characteristics
- We are capable of conducting the slit process in the clean room, and conducting the corona E process at the same time.
We can process up to one ton of Ø1,000 material.
Traverse slitting machines
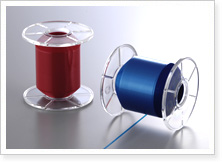
- 1)Uses
- Insulation film, carrier film for all types of processes
- 2)Characteristics
- We are capable of slitting traverse winding on ultra-narrow film (minimum width: 0.6 mm).
We also use a trapezoidal winding to prevent tape slackening, and can handle a maximum winding length of 20,000 m.
Other slitting machine
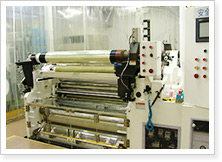
We have large slitting machine capable of corona processing in a Class 3000 environment to meet any customer requirement for cleanliness.
Slit process (Blade)
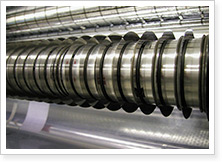
We use the share cut method.
We guarantee width accuracy that cannot be obtained with the laser cut method.
We grind all our blades in house to handle any type of film slits.
Blades for slitting
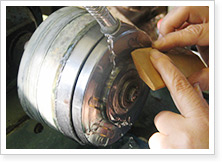
We grind our blades, the critical factor for slits, in house.
There is no device that can perform a satisfactory finishing and inspection. That’s why the processes from the finish grinding to the tooth tip for each individual item are done by hand.
Large slitting machine with corona processing
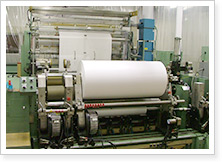
Corona processing is conducted on both sides of the film at the same time and slit to an optional width. Each individual film with discrepancies in material thickness is dealt with friction.
Corona processing
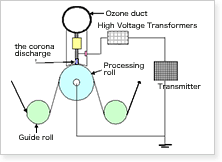
This technology improves the film surface by exposing the corona discharge to the processed film.
- Effects
- 1.Improved adhesion
- 2.Improved printing
- 3.Improved Vacuum Deposition characteristics
- 4.Improved coating characteristics
- 5.Change in degree of surface roughness
The above effects can be obtained.